Analysis of Bearing Capacity of Main Shaft Bearings in Large Wind Turbine Units
Release time:2025-04-25 hits:0次
Abstract: This article introduces the load conditions that the main shaft bearings of large wind turbines are currently subjected to, analyzes the influence of the main shaft bearing's offset load, lubrication, and clearance on the bearing capacity and service life, as well as the impact of the main shaft bearing's vibration on its own service life. It puts forward the key points, improvement suggestions, and recommendations that need to be paid attention to in the design.
Keywords: spindle bearings; Unbalanced load; Lubrication; Clearance; bearing vibration
The continuous increase in power of wind turbines brings about an increase in their volume and load, which puts higher demands on the reliability and safety of wind turbines. The main shaft bearings of wind turbines are the main components that absorb wind loads and transmit loads. Their performance not only affects the transmission efficiency, but also determines the maintenance cost of the main transmission chain. This article analyzes and studies the related issues of the bearing capacity of the main shaft of large wind turbines.
1. Load situation of wind turbine main shaft bearings
At present, the design concept of the transmission chain of wind turbines is to absorb as much load as possible from the main shaft bearings acting on the wind turbine, including radial force, axial force, and bending moment. After absorbing most of the unfavorable loads on the subsequent gearbox and generator through the main shaft bearings, only the favorable torque is transmitted to the high-speed end of the wind turbine. Therefore, higher requirements have been put forward for the service life of the spindle bearings. The arrangement of the main shaft bearing transmission chain mainly includes single point support, double point support, etc. The types of bearings used are not the same, but the ultimate goal is to only transmit torque to rotating components such as gearboxes or generators. Bearings need to withstand the effects of radial force, axial force, and bending moment. Therefore, for different layout forms, the type of bearing and the type of load it will bear should be considered when selecting.
Figure 1 shows the time series of wind speed. Because the wind speed will constantly change over time, the load will also change accordingly, and its repeated impact on the bearing will ultimately lead to bearing failure. Due to the instability of wind, some wind fields have extremely high turbulence effects, and at extreme wind speeds, wind loads have a stronger ability to damage wind turbine components. Therefore, improving the bearing capacity and service life of bearings will not only enhance the stability of the unit to a certain extent, but also significantly reduce maintenance costs.
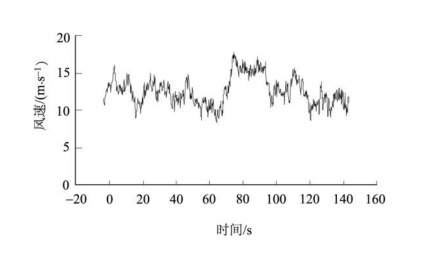
Figure 1 Time series chart of wind speed
Analysis of Bearing Capacity of Spindle 2
2.1 Analysis of Unbalanced Load Situation
At present, spindle bearings mainly include tapered roller bearings, self-aligning roller bearings, and three row cylindrical roller bearings. In order to provide longer service life and stronger load-bearing capacity, two or three row roller bearings are often arranged. When designing roller bearings, factors such as bearing clearance, roller shaping, and lubricant selection are mainly considered. For traditional transmission chains, the main shaft connected to the main shaft bearing is often relatively long, and the center of the wind turbine is far away from the main shaft bearing, which will generate a certain additional bending moment. Although the main shaft is a relatively rigid component, it may deform due to the action of the load. In this way, the inner and outer rings of the bearing connected to the main shaft are not on the same axis, resulting in a certain inclination angle and bearing bias. Figure 2 shows the roller stress distribution of two columns of self-aligning cylindrical roller bearings under a certain operating condition. As shown in Figure 2, the load distribution of the two column cylindrical roller bearings is basically symmetrical, indicating that the contact stress of the bearing components is relatively uniform under this working condition, and the operation is good. In the case of sufficient lubricating oil, there will be no temperature rise. But in another working condition (as shown in Figure 3), the contact stress of the loaded rollers in one column is relatively small, while the contact stress in the other column is relatively large. In this working condition, unilateral loading is severe, which may cause one column of the bearing rollers to roll and the other column to slide. The distribution of the lubricating oil film may also be uneven, and the bearing components may directly contact each other, causing the bearing to accelerate heating and the oil film to become thinner, resulting in poor lubrication of the bearing components and exacerbating bearing wear.
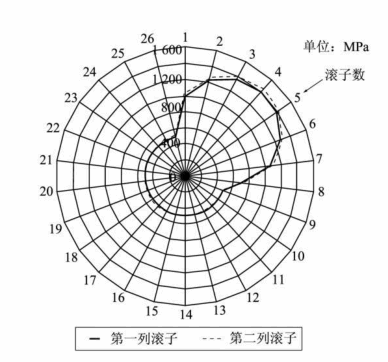
Figure 2 Distribution of contact stress on bearing rollers (under uniform load)
The main reason for the occurrence of excessive load on a single row of spindle bearings is the bending deformation of the spindle and the elastic deformation of the bearings and bearing seats themselves. The arrangement of bearings with long axes is particularly unfavorable for uniform bearing load distribution. Therefore, as much as possible, the main transmission chain adopts a short shaft arrangement to shorten the distance between the bearing and the wind turbine center, and improve the stiffness of the main shaft to reduce bending deformation. This is beneficial for reducing the bending moment attached to the bearing, making the bearing load as uniform as possible, and improving the service life of the bearing.
2.2 Lubrication and Bearing Clearance Analysis
The lubrication, operating temperature, and clearance of bearings have a significant impact on their load-bearing capacity. Appropriate lubricants can provide good lubrication between bearing components, especially under low temperature conditions. Lubricating oil is required to have good viscosity temperature characteristics, which can reduce the friction torque during bearing start-up. At the same time, lubricating oil is required to have certain resistance to water dilution. In order to prevent damage to the lubricating oil film, avoid direct contact between components, and prevent dry friction, bearing temperature rise and expansion, and reduce component performance, centralized lubrication can be considered to lubricate the bearings to prevent insufficient lubrication caused by long oiling cycles, which can lead to bearing damage.
Excessive bearing clearance can lead to a reduction in the number of rollers that can withstand external loads during operation, exacerbating roller pitting and wear; Too small clearance can easily lead to bearing friction heating, temperature rise, and damage to the oil film. In many extreme working conditions, only a few rollers are often loaded, and most rollers are in a relaxed state. Therefore, the influence of bearing clearance on its service life should be considered when designing and selecting.
2.3 Bearing vibration analysis
The wind speed and direction are constantly changing, and due to the corresponding aeroelasticity, the wind turbine is prone to twisting and swinging, and the transmission chain may also experience twisting and swaying phenomena. The bearing system (including the bearing seat), as a subsystem of the transmission chain, is actually an elastic damping dynamic system. Wind turbines are prone to regular torsional and pendulum vibrations under stable wind conditions, and bearings may also experience vibrations to some extent. Due to torsional vibration, the rollers wear the cage regularly, and the material ground on the cage falls into the lubricating oil, which accelerates bearing wear. To reduce bearing vibration, we can start by increasing the damping of the entire transmission chain to improve the stability of the transmission system. When selecting the transmission chain and bearings, we should consider the natural frequencies of the unit transmission chain and the entire machine to avoid low-frequency resonance between the natural frequencies of the transmission chain and external excitation frequencies.
3 Conclusion
From the perspective of wind turbines currently operating in wind farms in China, the main shaft bearings are damaged not only due to materials and processing techniques, but also because double row main shaft bearings are subjected to long-term single row eccentric loads under extreme wind speeds, resulting in damage to the bearing raceway and cage, inadequate lubrication leading to bearing component wear, improper clearance design causing bearing failure, and accelerated bearing wear caused by vibration. Due to the complexity of wind turbines and their loads, further research is needed to improve the load-bearing capacity of the main shaft bearings.